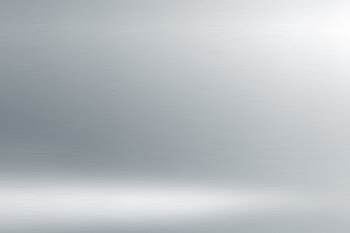
Raw material plays a critical role in producing MEDICAL implant and device components. The same properties that make machining difficult also make these materials corrosion and wear resistant, biomedically compatible and well suited to welding and temperature fluctuations.
Medical applications use titanium and cobalt alloys of Ti-6AI-4V or Ti-6AI-4V ELI, and ceramics are hard materials, while 316LVM stainless steel and PEEK are soft and more pliable. Some materials, like PEEK are like a Twizzler – the tools are easily “gummed up” and it’s difficult to cut. You end up pinching the candy rope instead of a good clean cut. Now cut a LifeSaver. The candy shatters leaving shards and ragged edges and ruining the knife in the meantime.
Machinists must balance the need for these difficult materials with the reality of machining it. All while maintaining high quality AND cost effectiveness.
The right machine is needed. While most any machine can produce a high precision part, the difference is seen when comparing quality and cost. A high precision part made on the wrong machine yields inconsistent quality, wasted raw material and higher prices for the customer.
Machinists also consider the play between machine, tools and material. The geometry of the part and the behavior of the raw material during machining impact their tooling and programming decisions.
While machinists may always prefer the “free machining” materials like 303 stainless steel, there is no substitute when producing medical components. Those tough materials are exactly what the doctor ordered.